The whisper of the spinning loom during the Industrial Revolution signaled a powerful change in how we made things. Fast forward a few centuries, and we stand at the edge of yet another revolution. But this time, it’s not just machines – it’s screens, data streams, and dynamic digital signage leading the charge into Industry 4.0. By integrating lean strategies with agile practices, digital signage is setting manufacturers up for a dazzling future, enhancing monitoring capabilities, managed services, and automation.
Understanding How Digital Signage Impacts Industry 4.0
Industry 4.0 represents the golden age of digital manufacturing, where every gear and widget is connected and intelligent. But beyond just machines, consider the power of digital signage, which visually communicates critical data. It helps users anticipate disruptions, facilitates automation, and optimizes workflows by providing real-time data visualization.
“In modern manufacturing environments, working smarter with data intelligence is a necessity, as it drives better decision-making, increases efficiency, and provides a competitive edge. Radiant Technology Group helps you digitize, visualize, analyze, collaborate and remediate critical information so your organization can effectively harness the power of data intelligence.”
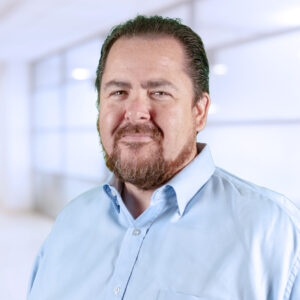
Dive deeper, and you’ll see that Industry 4.0 melds the physical with the digital, leaning on technologies like IoT, AI, robotics, and digital signage. For manufacturers, this union promises astronomical boosts in productivity, efficiency, and customization.
Digital Signage in Smart Manufacturing
One of the most distinct characteristics of Industry 4.0 is the integration of smart systems. Machines no longer operate in isolation; they’re interconnected, sharing data adapting to changes, and making decisions in real-time. With advanced sensors and analytics, factories can predict and prevent equipment failures, optimize supply chains, and respond flexibly to shifts in demand. This predictive maintenance alone can save businesses a significant amount of money.
At Radiant Technology our team of experts develops digital solutions that streamline workflows and connect your teams to actionable information to drive operational improvements and efficient environments. This allows for better data visualization, access to real-time metrics and collaboration tools. With Radiant Technology as your partner in continuous improvement, your smart manufacturing environment works for you, allowing your teams to agilely make decisions that impact the bottom line.
Customization and Flexibility
In traditional manufacturing setups, product lines are typically static, making it a daunting task to switch between product variants. With Industry 4.0, however, production lines are agile. They can adapt and reconfigure based on real-time data. For consumers, this translates into greater product customization without a steep increase in cost. With data consolidation, Radiant Technology is able to consolidate vital operational data to a single source, giving teams greater visibility of real-time metrics with automated calls to action. You’re able to proactively address issues and accelerate decisions to stay competitive and optimize operations. Our experts devise digital blueprints that enhance workflows and equip teas with actionable insights, allowing for continuous improvement. Experience improved data visualization, instantaneous metric access and unparalleled collaborative tools when you partner with Radiant Technology.
Boosting Productivity and Efficiency with Digital Signage
Industry 4.0 also heralds an era of unprecedented productivity. Smart systems ensure that resources, whether it is materials or energy, are used optimally. AI-driven insights can streamline operations, reducing waste, and ensuring that every action taken adds value. Manufacturers can anticipate challenges, from equipment malfunctions to supply chain disruptions, ensuring smooth and efficient operations, all visualized with digital signage.
By monitoring systems with Radiant Pulse, we’re able to proactively address issues and accelerate remediation, ensuring your systems are functional and providing a comprehensive overview of the manufacturing floor, no matter where you are.
The Focus Ahead
With such a large dynamic shift, companies will need to pay particular attention to protecting assets, ensuring there is a plan in place, and focusing on end user adoption.
- Cybersecurity: With an increased reliance on interconnected systems, vulnerabilities can arise. Protecting intellectual property, personal data, and operational processes from cyber threats is paramount.
- Investment: Transitioning to a smart factory demands significant capital. The return on investment, though lucrative in the long run, requires patience and vision. Partner with Radiant Technology for road mapping and Blueprint services. Maximize your time, planning, and set a clear and documented vision for resources.
- Cultural Shift: Integrating new technologies can be a cultural shock for many employees. Companies must invest in training and foster a culture that’s open to change.
The Future is Now
Industry 4.0 is not a distant dream-it’s unfolding before our eyes. As manufacturers embrace this digital shift, the entire ecosystem, from suppliers to consumers, stands to benefit. It’s an exciting time, filled with promise and potential. And while the journey may pose challenges, the rewards of a connected, responsive, and efficient manufacturing sector are well worth the effort.